I have been thinking (never a good sign as it usually means changes are afoot) about my lack of stiffness (well, I am getting on a bit).
The thought of cutting the body about and making lots of carbon fibre panels doesn't fill me with joy and excitement. So I have been rethinking the problem and have almost decided to go the full roll cage route instead. These photos added a little spur to the thought process:

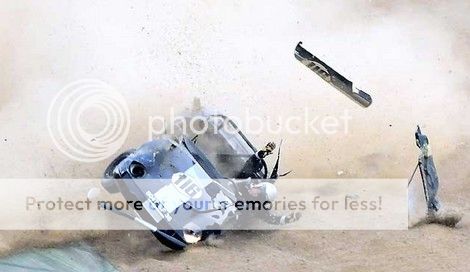
Tony Tompson are the sole supplier of the Safety Devices FIA approved roll cage and is the only one available in the UK. I found one in Europe, but more expensive and heavier. Safety Devices cage shown below:

Only issue is that the side bars sit in the void under the doors. OK on the driver's side but the passenger's side is full of silencer. As these bars are separate modifying one shouldn't be a problem.
The thought of cutting the body about and making lots of carbon fibre panels doesn't fill me with joy and excitement. So I have been rethinking the problem and have almost decided to go the full roll cage route instead. These photos added a little spur to the thought process:

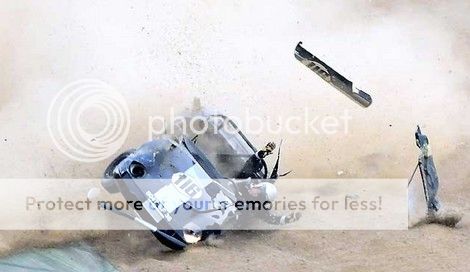
Tony Tompson are the sole supplier of the Safety Devices FIA approved roll cage and is the only one available in the UK. I found one in Europe, but more expensive and heavier. Safety Devices cage shown below:

Only issue is that the side bars sit in the void under the doors. OK on the driver's side but the passenger's side is full of silencer. As these bars are separate modifying one shouldn't be a problem.