Been spending a fair bit of time designing dash switch panel. As it will be the signature piece of the interior I need to get it right (to my satisfacion).
To that end I will be getting it made by my favourite CNC man. I don't have the necessary cutting tools or skills to produce it to the standard I require.
I started off with the switches on the centre console but a lack of room and conflict with my left arm/hand killed that idea.
My previous dash had a flip down centre section into which I had fitted 5 gauges so I decided to pay homage to this. No gauges however, only switches. The original panel is just visible in the photo below.
The design has gone through many iterations. This is one of the early designs.
I settled on this design.
I then realised that the key fob would interfere with the switches so back to the drawing screen.
Unless I think of something else, this is the final design. I have built in redundant switches and a warning lamp to cover future upgrades or something I have forgotten.
I have had to use two conventional black toggled switches as I couldn't find them with the functions I required in the lluminating style of the switches below them.
The design was constrained by the physical shape of the various switches.
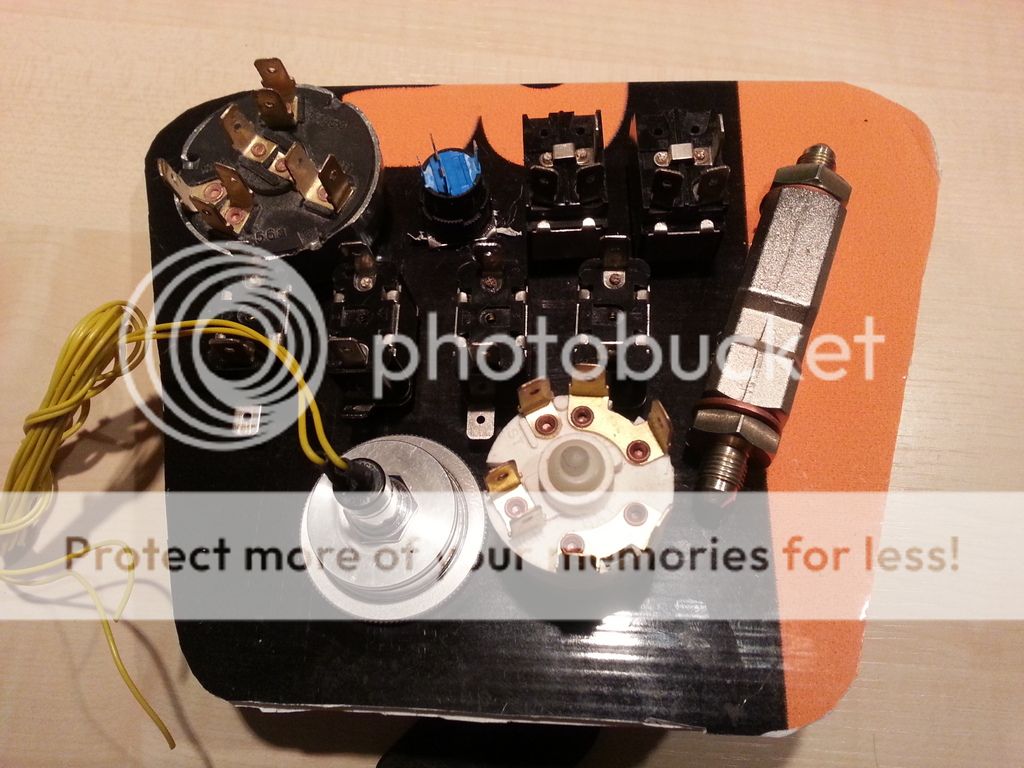