Gloss or Matt, that is the question.
I have been agonising over body colour and finish for a couple of years. When I broke it in 1984 it was gloss black and I still like black. Around 10 years ago I thought about doing it matt black, but then the 'murdered' look became all the rage so I couldn't do that. What? Follow the crowd? No way.
Since then I have been through every colour and effect there is, but keep coming back to black.
I thought that I had cracked it last year. I fancied a fade from dark grey to black from front to back. However, I didn't want any transition lines, it had to be a perfect continuous transition. A couple of painters have claimed that they could do it, for a king's ransom.
I looked into wraps, but no one that I have so far talked to can supply it. Another problem is that wrap comes 1.52m wide and my car, from the bottom of the wheel arches, is 1.7m with no panel lines.
The interior is going to be matt black so maybe I should do a matching exterior.
A quick and dirty rattle can trial:
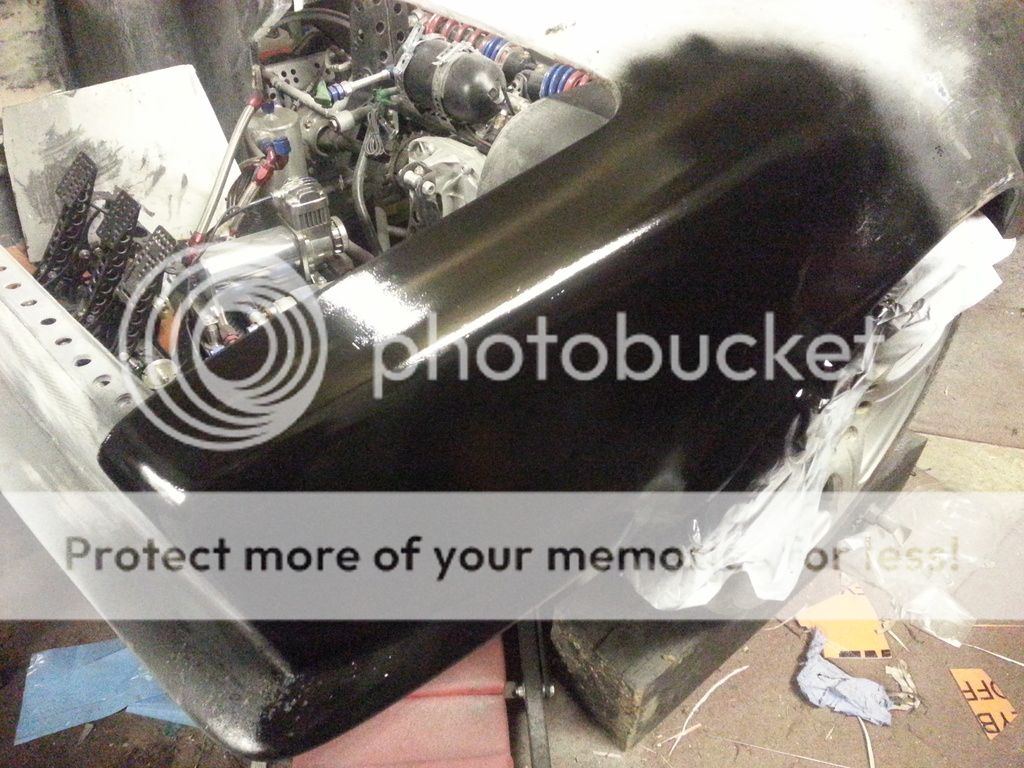